Rotary screener, also known as rotary sieve, is an essential process machine for granulate and powder separation in various industries. It is a cylindrical-shaped device that rotates on a horizontal axis, and its primary function is to sift, sieve, or grade materials effectively. Rotary screeners are common in industries such as agriculture, food processing, chemical, and mining, among others.
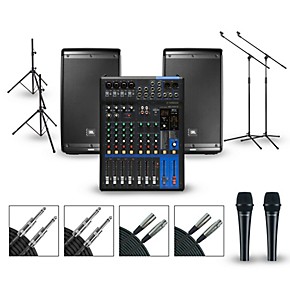
The granulate and powder separation process is crucial for many organizations, as it ensures consistent quality and purity of the final product, enhances productivity, and minimizes waste. Rotary screeners use a perforated screen or mesh to separate materials based on size, shape, and weight. The screen's perforations determine the size of the particles that pass through, while the rotary motion ensures uniform distribution and accurate separation.
Customized Rotary Screeners
The design of rotary screeners varies based on the industry, process, and the particular product being separated. Customization allows the machine to meet specific demands and requirements, resulting in increased efficiency and productivity. Customizable features include the screen size and shapes, the speed of rotation, the material used for construction, and the discharge rate.
Rotary screeners with large diameter screens and high-speed rotation are ideal for large production output and handling of heavy-duty materials. The screens' shapes can be round or rectangular, and the perforations can be punched, drilled, or laser cut to provide varying hole shapes and sizes. Different materials can also be used to construct the screen, depending on the material being sieved, such as stainless steel or nylon.
The discharge rate is another customized feature that can be adjusted for different materials and processes. The discharge rate determines the amount of material that passes through the screen per unit time, which affects the efficiency and effectiveness of the machine. A rotary screener with a high discharge rate is ideal for quick and continuous material separation.
Benefits of Rotary Screening
Rotary screening provides various benefits that significantly impact different industries' success and productivity. Some of the benefits of rotary screening include:
1. Consistent Quality: Rotary screeners ensure the final product's consistency by separating the granulates and powders based on size, shape, and weight. This ensures the entire batch remains of equal quality and eliminates issues such as over-sizing or undersizing particles.
2. Increased Efficiency: Rotary screeners improve productivity by ensuring a more comprehensive separation process that produces high-quality granulates or powders faster. This enhances the overall efficiency of the production process.
3. Reduced Waste: Efficient separation of materials means a reduced waste production, which is crucial for the environment and overall profitability.
4. Cost-Effective: Rotary screening saves both time and resources as it eliminates manual screening processes that are labor-intensive.
Conclusion
In conclusion, rotary screeners are an essential process machine for granulate and powder separation. Customization of the machine ensures it meets specific requirements, resulting in increased efficiency, productivity, and consistency in the final product. Rotary screening has various benefits, including improved efficiency, reduced waste production, and a cost-effective process. Rotary screening is a valuable investment for any organization seeking to improve its granulate and powder separation process.