Working principle
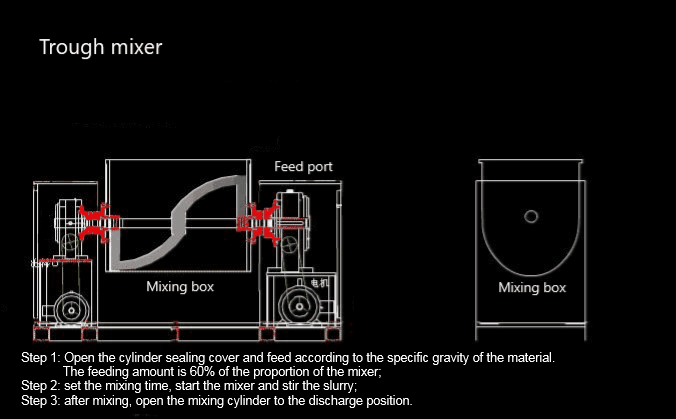
Main structure
The Notch Shape Mixer is mainly composed of five components: 1. Mixer Reducer The mixer reducer is the main transmission structure of the slot mixer, which is located on the right side of the slot mixer, and the motor installed in the base machine drives the worm and worm gear through the triangle belt during work, and drives the mixer with a deceleration of 1:40. The worm wheel shaft is hollow and equipped with fixed keys, which allows the mixing paddle to be freely loaded and disassembled. The top of the reducer is equipped with 2 ring screws for installation, disassembly and installation. The end cap is equipped with a screw for the positioning of the high-speed mixing paddle, which has been adjusted at the factory and generally does not need to be adjusted in use. 2.Mixer Groove The groove mixer is u-shaped, made of stainless steel, equipped with a mixing paddle, which lies horizontally on the mixing reducer and the pouring reducer. 3. Discharge Reducer The discharge reducer is to control the positioning angle of the mixing tank, which is located on the left side of the trough mixer, and when working, the motor installed in the frame drives the worm and worm gear through the V-belt, driving the mixing groove to rotate in a certain angle range, so that the mixed material is poured out at once. 4. Frame And Motor Unit The base is an overall structure, the motor is installed on the movable board on both sides of the slot mixer base, and the upper and lower parts of the motor can be adjusted by screws, so that the V-belt can get a certain tightening and maintain the transmission of power. 5. Electrical Control Box The electrical control box is to control the movement of the slot mixer.Features
1. The volume can be customized, the mixing effect is good, and the uniform mixing degree of the material can reach more than 99.5%. 2. The mixing method can be configured with different mixing rod shapes according to different materials, such as single and double screw belt or screw belt + throwing knife 3. The stirring effect of low energy consumption is more suitable for the chemical reaction of the material 4. A variety of closed feeding methods are preferred for feeding, and the caliber can be seamlessly closed 5. The discharge method is reasonable and efficient, so as to achieve no residue of the material, and the discharge is more thorough and stable 6. Realize the efficient mixing of powder-liquid mixing, powder-powder mixing and powder-solid powder, which is especially suitable for material mixing with high mixing uniformity requirements and large material specific gravity difference.Product advantages
● Good dispersion: The equipment completely solves the problems of low uniformity and dead angle caused by the different proportions of materials. This equipment adopts a mixed structure of five-axis with flying knife mortar, which can effectively disperse various staple fibers. ● Wide range of use: The equipment can meet the production of dry mortar with different performance requirements. Such as: masonry mortar, plaster mortar, polymer mortar required for thermal insulation system, polystyrene particle moisturizing mortar and other dry powder mortar. ● Small investment: The device has obvious price advantages. Small investment, quick results. ●Simple and convenient to use: the equipment has a small footprint, simple operation, low energy consumption, and can produce 5-8 tons per hour. ●Long service life: The vulnerable parts of this equipment are all made of high-strength wear-resistant steel as parts. It has the characteristics of long service life.Technical parameters
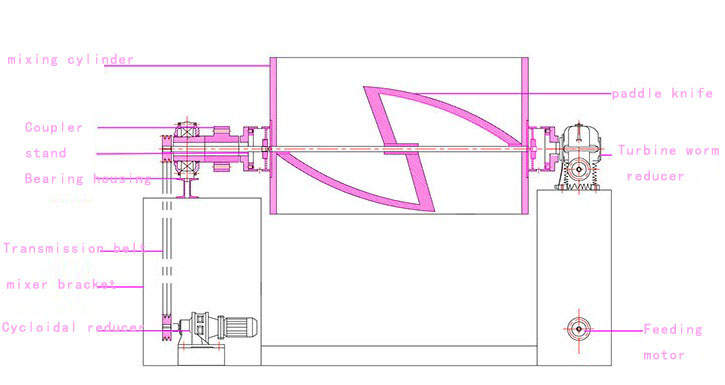
Model | Volume(m3) | Feeding quantity(kg/second) | Overall dimension (mm) | Mixing time(min) | Stirring speed(r/min) | Motor power(kw) | Discharge motor power(kw) |
CF-CXM-50 | 0.05 | 38 | 1300*1000*540 | 6-15 min | 28 | 1.5 | 0.55 |
CF-CXM-100 | 0.1 | 83 | 1400*1100*600 | 6-15 min | 26 | 2.2 | 0.55 |
CF-CXM-150 | 0.15 | 124 | 1360*1120*600 | 6-15 min | 24 | 3 | 0.55 |
CF-CXM-200 | 0.2 | 140 | 1460*1200*600 | 6-15 min | 24 | 4 | 0.55 |
CF-CXM-300 | 0.3 | 210 | 1820*1240*680 | 6-15 min | 24 | 5.5 | 1.5 |
CF-CXM-400 | 0.4 | 310 | 2000*1240*780 | 6-15 min | 20 | 5.5-6 | 1.5 |
CF-CXM-500 | 0.5 | 350 | 2150*1240*780 | 6-15 min | 18 | 6-7.5 | 2.2 |
CF-CXM-750 | 0.75 | 560 | 2200*1240*780 | 6-15 min | 16 | 7.5-6 | 2.2 |
CF-CXM-1000 | 1 | 780 | 2300*1260*800 | 6-15 min | 16 | 11-6 | 3 |
CF-CXM-1500 | 1.5 | 1150 | 2500*1300*860 | 6-15 min | 12 | 11-6 | 3 |
CF-CXM-2000 | 2 | 1500 | 2600*1400*940 | 6-15 min | 12 | 6-15 | 4 |
CF-CXM-2500 | 2.5 | 2100 | 3000*1560*1160 | 8-20min | 12 | 5-6 | 5.5 |
CF-CXM-3000 | 3 | 2250 | 3800*1780*1500 | 8-20min | 10 | 6-12 | 7.5 |
Product Details
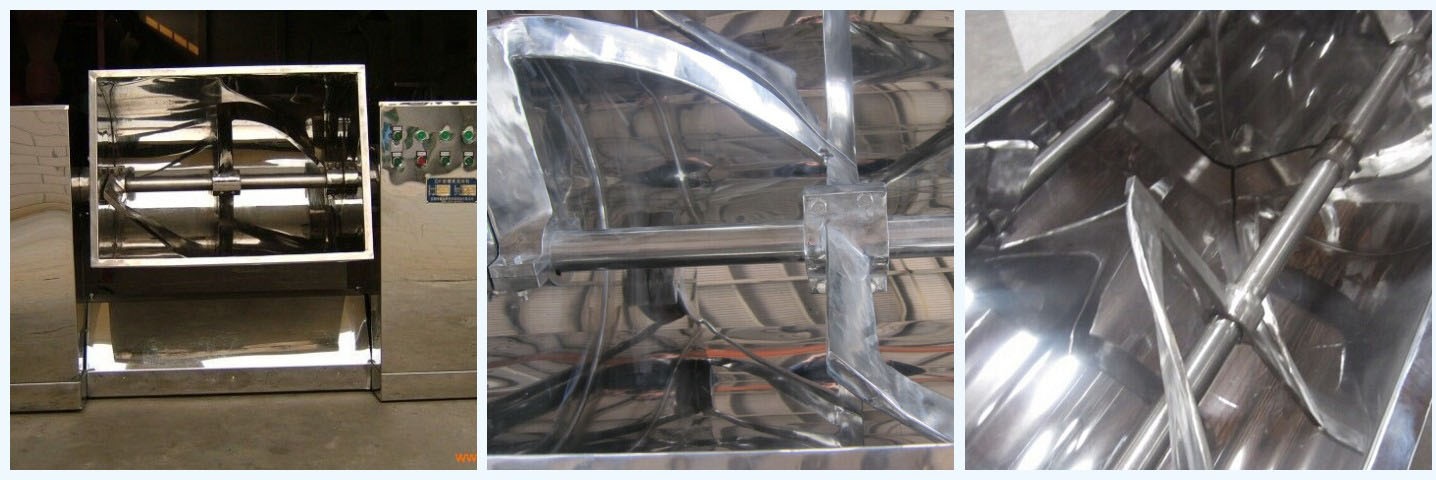