Working principle
Dewatering screen is mainly used for dehydration, desliming and de-intermediation. It can be used for sand washing in sand and gravel plant, coal slime recovery in coal preparation plant, dry discharge of tailings in mineral processing plant, etc., so it is also called sand and gravel dewatering screen, mine dewatering screen, Coal slime dewatering screen, tailings dry discharge screen, high frequency dewatering screen, etc. The dewatering screen adopts dual-electrode self-synchronization technology, which is composed of screen box, vibration exciter (or vibration motor), support system and motor. The two unconnected vibrators are driven by the belt coupling for synchronous and reverse operation. The centrifugal force generated by the two sets of eccentric masses is superimposed along the vibration direction, and the reverse centrifugal force is counteracted, thereby forming a single excitation vibration along the vibration direction. , so that the screen box does a reciprocating linear motion. According to the washing and dewatering requirements of different materials, the dewatering screen is designed with different screen inclination angles and screen plate forms to improve the dewatering production efficiency and ensure the dewatering effect. The dewatering screen can be installed on the left or right of the excitation source according to the location of the production site, which is convenient for the layout of the production process. The dewatering screen dewaters and drains the tailings slurry, such as the mixed slurry of coal slime, to reduce the energy loss of the dryer.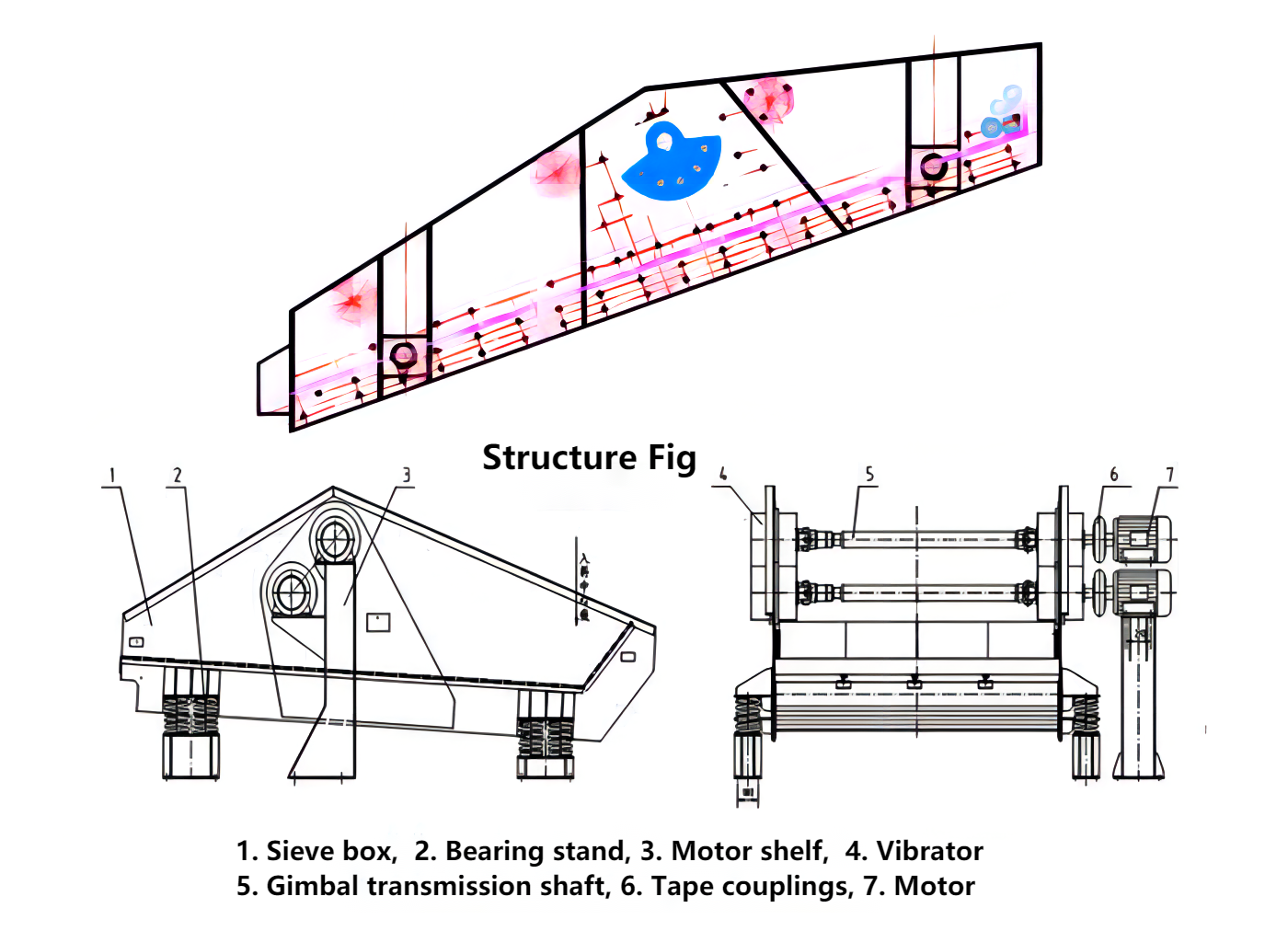
Product advantages
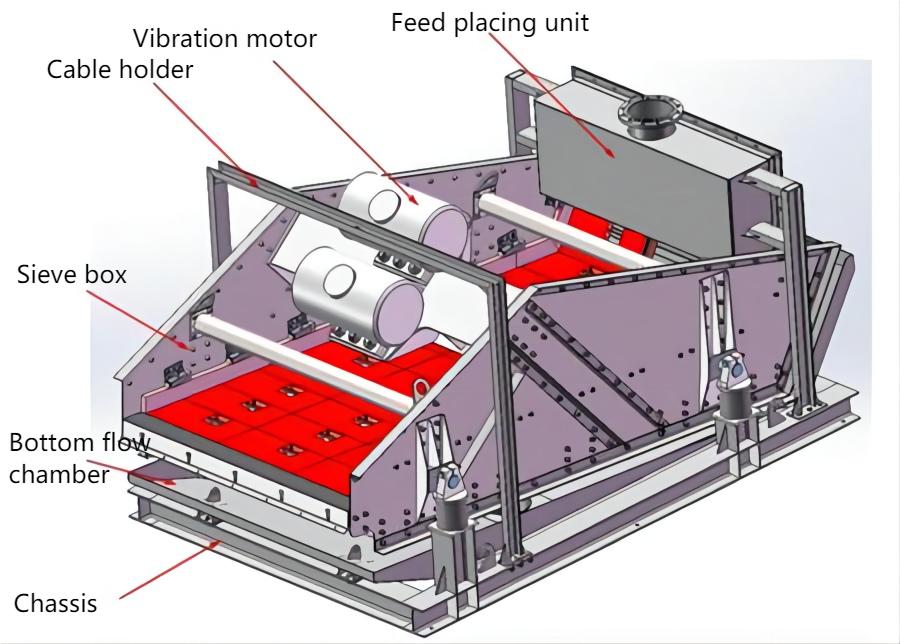
Technical parameters
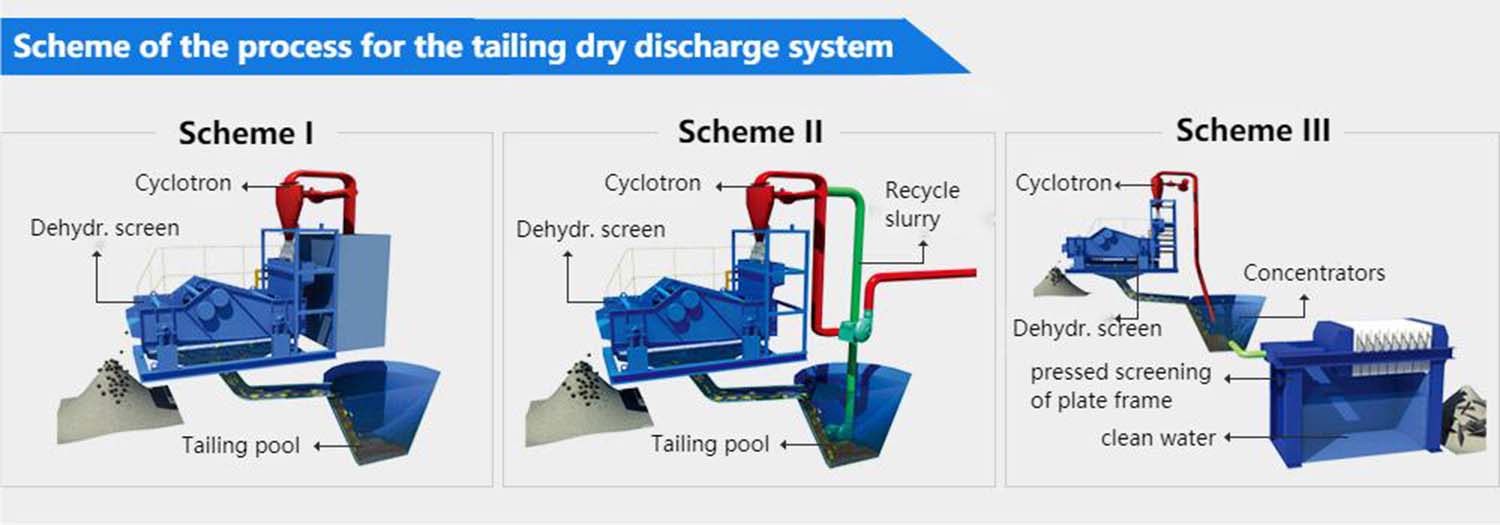
Model | Screen area(m³) | Motor power(kw) | Processing capacity(m³/H) | Feed particle size(MM) | Overall dimension(MM) | Weight(t) |
CF-TSS0720 | 1.4 | 0.75*2 | 5-10m³ | ≤10 | 2300*1000*750 | 0.8 |
CF-TSS9020 | 1.8 | 1.1*2 | 10-20m³ | 2300*1200*750 | 1.2 | |
CF-TSS1020 | 2 | 1.1*2 | 10-30m³ | 2300*1300*750 | 1.6 | |
CF-TSS1225 | 3 | 1.5*2 | 50-80m³ | 2800*1200*800 | 2.1 | |
CF-TSS1230 | 3.6 | 2.2*2 | 60-90m³ | 3300*1500*800 | 2.6 | |
CF-TSS1530 | 4.5 | 3*2 | 100-120 | 3300*1800*800 | 3.2 |
Product details
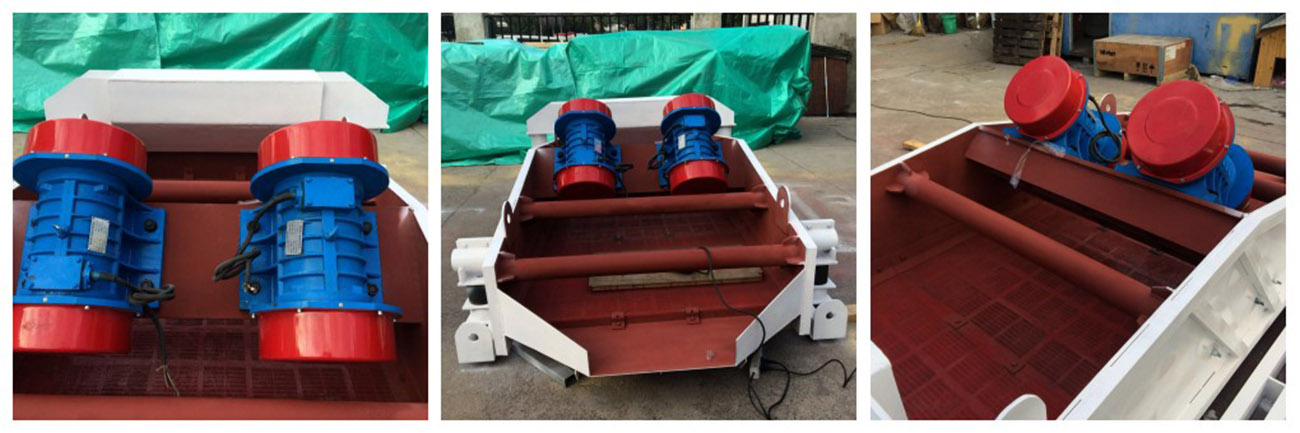
Application range
Mine dewatering screen is a special vibrating screen for coal slime dewatering operation. It is widely used in coal preparation, electric power, mineral processing, salt production, chemical industry, sugar production and other industries. Coarse, filter press, dewatering of other ultra-fine materials, filtration, coarse dewatering, de-intermediation, desliming and recovery processes. Application material Iron tailings, gold tailings, copper tailings, graphite tailings, quartz sand, zircon sand, glass sand, construction sand, foundry sand, coal slime dewatering municipal sewage, industrial sewage, solid-liquid separation of river sludge, sewage Filtration of treatment plants. Conditions of use of mine dewatering screen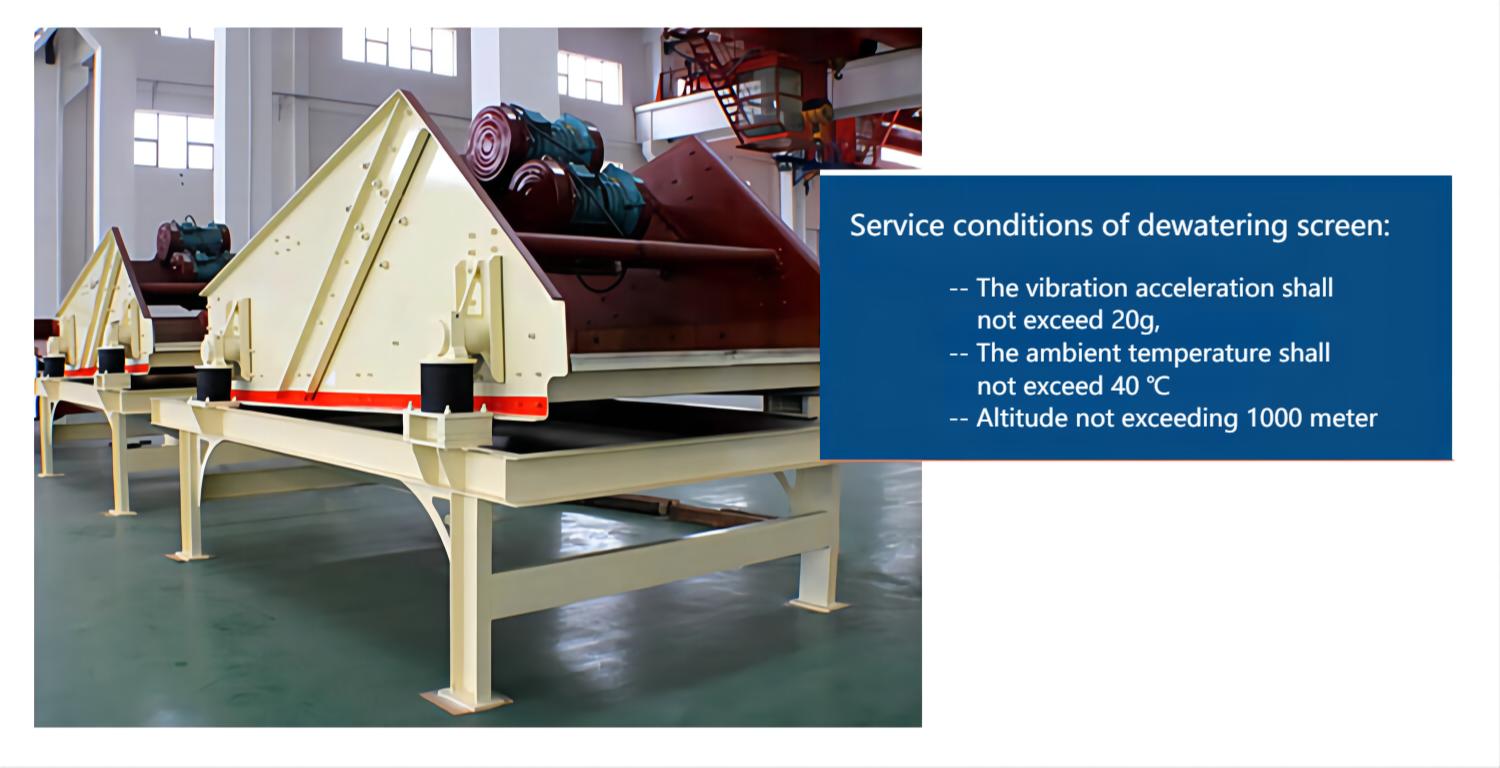