Working principle
The ultrasonic vibrating screen machine is composed of two parts that resonate with the ultrasonic system and the vibration motor system. Its essence is to add a high-frequency vibration to the traditional vibrating screen to increase the acceleration of the material, effectively solve the adsorption of the material on the screen, and let the material pass through the screen quickly. Among them, the ultrasonic system is composed of generator, transducer, resonance ring, and high-frequency connecting line, and the vibration motor system is composed of upright vibration motor and mechanical body, screen mesh, shock absorption and so on.
The high-frequency electrical oscillation generated by the ultrasonic generator (power supply) in the ultrasonic system is converted into high-frequency ultrasonic waves by the transducer. These ultrasonic waves are transmitted to the resonant ring to resonate the resonant ring, and then the resonant ring transmits the vibration evenly to the screen surface. . The materials on the screen are subjected to low-frequency three-dimensional vibration, and ultrasonic vibration is superimposed, which can not only effectively prevent mesh blockage, but also improve the screening output and quality, and solve the problem of strong adsorption, easy agglomeration, high static electricity, high density, Screening problems such as light weight and specific gravity. Achieve big results in performance.
CF series ultrasonic vibrating screen has high screening accuracy, and the output can be increased; industrial fine production screening needs above 600 mesh!
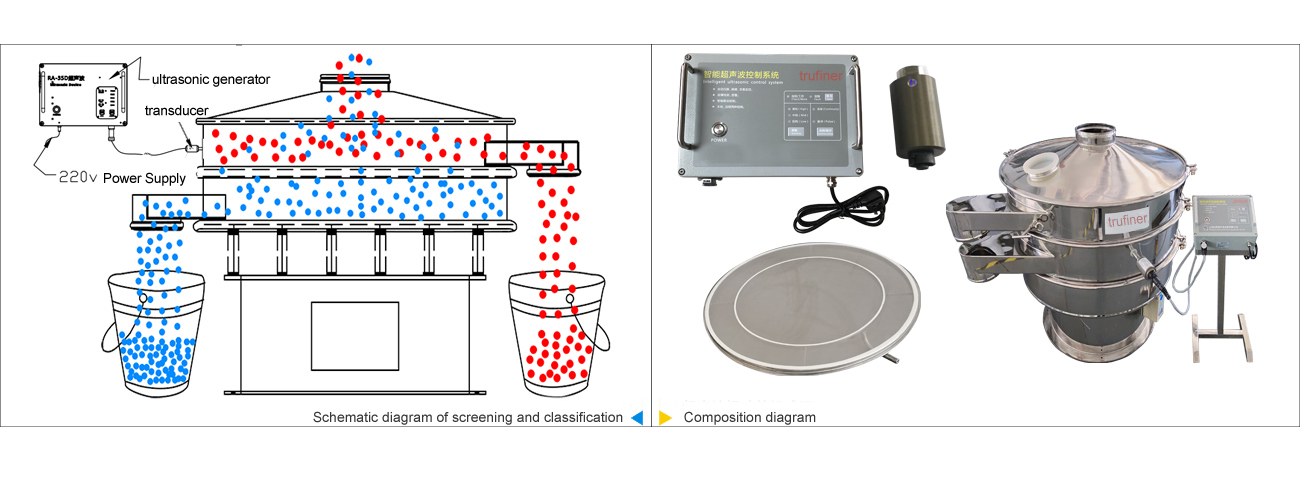
Ultrasonic vibrating screen is a simple, practical and reliable screening system, and it is an effective solution to the current mesh blockage and embedding. It can be widely used in pharmaceutical, metallurgy, chemical, mineral processing, food and other industries that require fine screening and filtration. It has high screening and filtration accuracy and can effectively solve the screening due to agglomeration, static electricity, and strong adsorption.
Product features
1. It is suitable for sieving of 10~300μm mesh, and the production capacity can be increased by 10 times.
2. Prevent the clogging of 50~625 mesh meshes and the plugging of side-by-side particles to the meshes, eliminate the screen damage caused by the mechanical vibration system, reduce the load of the screen, effectively clean the mesh, and prolong the life of the precious material screen. service life.
3. Accelerate the melting and separation of agglomerates, thereby increasing the screening capacity, reducing the presence of large-size sieves, and easily separating fine particles with adjacent diameters without adding any other screen cleaning devices.
4. Ultrasonic assisted screening is physical screening, does not change the characteristics of materials, is suitable for screening new materials, does not increase the temperature of materials, and can work continuously, especially suitable for materials with temperature control requirements such as: drugs and Raw materials, thermosetting coatings industry, etc.
Product advantages
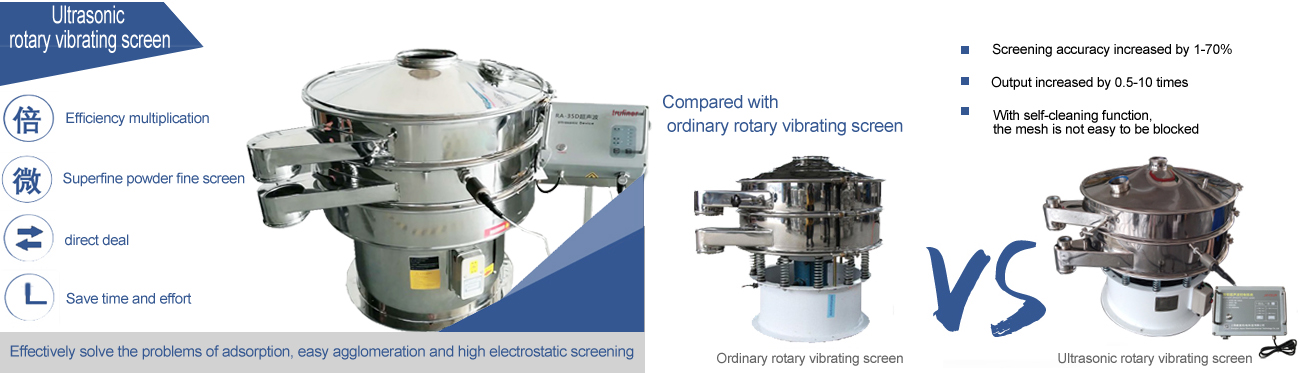
Compared with ordinary vibrating screen, ultrasonic vibrating screen:
It superimposes a high-frequency vibration on the traditional vibrating screen to make the acceleration of the material faster, effectively solve the adsorption force of the material on the screen, let the material pass through the screen quickly, and solve the problem of difficult screening.
● Fine screening
It solves the screening problems of materials with strong adsorption, easy clumping, strong viscosity, high static electricity, high density, ultrafine powder and other characteristics.
● Improve efficiency
The screening accuracy can be increased by more than 80%, and the output can be increased by 2 to 5 times.
● Low cost
The pollution and wear of powder caused by conventional screening methods are changed, and the noise of the screening machine is greatly reduced.
No need to add screen cleaning equipment, except for screen damage usually associated with mechanical cleaning equipment, increasing the life of the screen
● Not easy to block the network
The vibration frequency of the ultrasonic vibrating screen is 360,000 times per minute, which can effectively prevent the screen from clogging, and the materials that are difficult to screen hardly block the screen.
Comparative analysis of test materials between ultrasonic vibrating screen and ordinary vibrating screen
Model(mm) | Ordinary screening machine | Ultrasonic vibrating screen | |||
test material | Mesh | Test Results | mesh | Test Results | |
Φ1000 | Silicon carbide | 500 | Cannot be sieved | 500 | 1500KG/H |
Φ1000 | Tungsten carbide powder | 600 | 15 minutes without sifting out fine powder | 600 | 30KG/H |
Φ1000 | Vitamin C Powder | 400 | 1KG/H | 100 | 120-150KG/H |
Φ500 | pollen | 400 | 15 minutes without sifting out fine powder | 400 | 20% fineness is screened out in 15 minutes for finer and more effective grading |
Nickel powder, Cobalt powder | 325 | Sieve three times to meet the requirements | 400 | Sieve to meet the requirements at one time | |
Φ450 | NdFeB powder | 300 | 35% sieve residue in 30 minutes | 300 | 3% sieve residue in 30 minutes |
Technical parameter
Model | Outer frame diameter (mm) | Screen diameter(mm) | Maximum feed particle size(mm) | Screen mesh | Layers | Vibration times | Power(KW) |
CF-CXZS | φ600 | 560 | <10 | 2-800 | 1-5 layers | 1440 | 0.55 |
CF-CXZS | φ800 | 760 | <20 | 2-800 | 1-5 layers | 1440 | 0.75 |
CF-CXZS | φ1000 | 950 | <20 | 2-800 | 1-5 layers | 1440 | 1.1 |
CF-CXZS | φ1200 | 1150 | <20 | 2-800 | 1-5 layers | 1440 | 1.5 |
CF-CXZS | φ1500 | 1430 | <20 | 2-800 | 1-5 layers | 1440 | 2.2 |
CF-CXZS | φ1800 | 1700 | <30 | 2-800 | 1-5 layers | 1440 | 3 |
CF-CXZS | φ2000 | 1910 | <30 | 2-800 | 1-5 layers | 1440 | 4 |
Product details
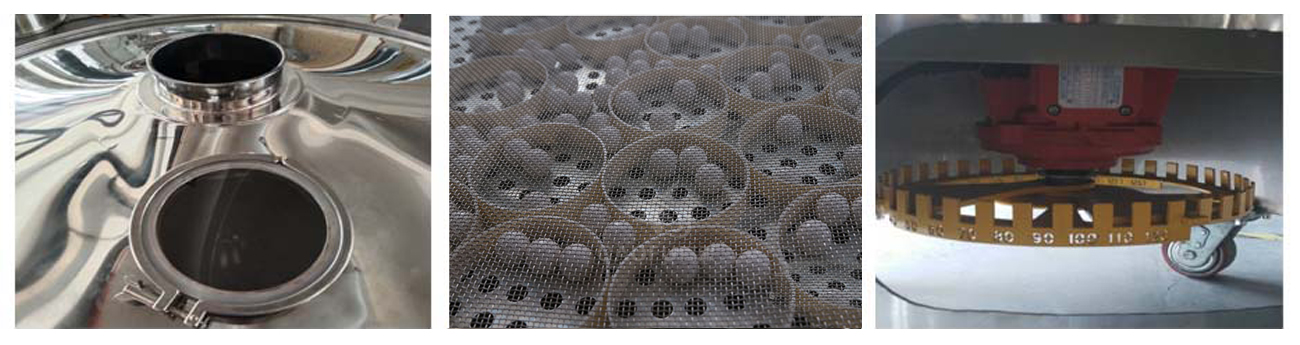